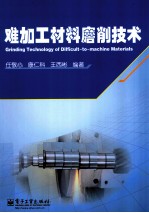
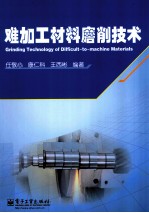
难加工材料磨削技术PDF格式文档图书下载
第1章 磨削的基本参数 1
1.1 磨削的特点 1
1.2 磨削参数 4
1.2.1 砂轮与工件的接触长度ls 4
1.2.2 砂轮有效磨刃数 5
1.2.3 一个磨刃的未变形切屑最大厚度agmax 10
1.2.4 当量磨削厚度aeq 14
1.2.5 砂轮当量磨削直径de 16
第2章 难加工材料的材料特性及磨削加工性的评定 17
2.1 常用难加工材料的分类和材料特性 17
2.1.1 钛合金 17
2.1.2 高温合金 20
2.1.3 金属间化合物基高温结构材料 23
2.1.4 超高强度钢 25
2.1.5 不锈钢 27
2.1.6 工程陶瓷 29
2.2 难加工材料磨削加工性的评定 32
2.2.1 以磨削力评定磨削加工性 33
2.2.2 以磨削温度评定磨削加工性 37
2.2.3 以磨削表面粗糙度评定磨削加工性 42
2.2.4 以磨削表面变质层评定磨削加工性 45
2.2.5 以磨削比评定磨削加工性 51
第3章 钛合金的磨削 56
3.1 钛合金的材料特性及磨削特点 56
3.1.1 钛合金的材料特性 56
3.1.2 钛合金的磨削特点 57
3.2 磨削钛合金的砂轮磨损 59
3.2.1 黏附磨损 59
3.2.2 磨粒的磨耗与破碎 63
3.2.3 扩散磨损 67
3.3 磨削钛合金的磨削力 69
3.3.1 黏附对磨削力的影响 69
3.3.2 黏附条件下的磨削力数学模型 70
3.3.3 钛合金磨削力的经验计算式 75
3.4 磨削钛合金的磨削温度 77
3.4.1 钛合金磨削温度场的理论计算 77
3.4.2 钛合金磨削表面温度及磨削温度场的测量 82
3.5 钛合金磨削表面完整性 86
3.5.1 表面粗糙度 86
3.5.2 磨削表层元素变化及气体杂质的污染 88
3.5.3 磨削表层的塑性变形 88
3.5.4 磨削表层显微硬度的变化 90
3.5.5 钛合金磨削烧伤表层的成分变化 92
3.5.6 磨削表层残余应力 92
3.5.7 疲劳性能 95
3.6 磨削钛合金的磨削液 97
3.6.1 钛合金对磨削液的要求 97
3.6.2 磨削液特性对磨削性能的影响 98
3.6.3 磨削钛合金的水溶性磨削液 99
3.6.4 磨削钛合金的磨削油 102
3.6.5 磨削钛合金的砂轮固体浸渗润滑剂 106
3.7 立方氮化硼(CBN)砂轮磨削钛合金 108
3.7.1 CBN磨料的性能及CBN砂轮的种类 108
3.7.2 陶瓷结合剂CBN砂轮磨削钛合金 110
3.8 钛合金的缓进给磨削 115
3.8.1 缓进给磨削的特点 115
3.8.2 钛合金缓进给磨削的磨削温度和磨削烧伤 117
3.8.3 钛合金磨削表层的残余应力 121
3.8.4 缓进给磨削中抑制烧伤的措施 122
3.9 磨削钛合金的砂轮参数及磨削加工用量的选择 127
3.9.1 砂轮的选择原则 127
3.9.2 磨削加工用量的选择原则 130
3.9.3 磨削加工用量和砂轮参数的选择 132
第4章 高温合金的磨削 139
4.1 高温合金的材料特性及磨削特点 139
4.1.1 高温合金的材料特性 139
4.1.2 高温合金的磨削特点 141
4.2 高温合金的磨削力和磨削温度 142
4.2.1 高温合金的磨削力 142
4.2.2 磨削高温合金的磨削温度及磨削温度场 146
4.3 磨削高温合金的砂轮磨损 151
4.3.1 磨削高温合金时砂轮表面的黏附 151
4.3.2 磨削高温合金的磨削比 152
4.4 高温合金磨削表面完整性 154
4.4.1 高温合金的磨削表面粗糙度 155
4.4.2 高温合金磨削后的表层硬度变化 158
4.4.3 高温合金的磨削残余应力 161
4.4.4 高温合金磨削表层的微观组织变化 164
4.4.5 磨削表面完整性对高温合金材料疲劳强度的影响 167
4.5 高温合金的缓进给磨削 176
4.5.1 高温合金的缓进给磨削烧伤 176
4.5.2 缓进给磨削工艺的合理应用 181
4.6 磨削高温合金的砂轮参数及磨削加工用量的选择 186
4.6.1 砂轮的选择原则 186
4.6.2 磨削加工用量的选择原则 188
4.6.3 磨削加工用量和砂轮参数的选择 188
第5章 超高强度钢的磨削 196
5.1 超高强度钢的性能和磨削特点 196
5.1.1 超高强度钢的性能 196
5.1.2 超高强度钢的磨削特点 198
5.2 超高强度钢的磨削力和磨削温度 199
5.2.1 超高强度钢的磨削力 199
5.2.2 超高强度钢的磨削温度 203
5.3 超高强度钢的磨削烧伤及其判别方法 205
5.3.1 超高强度钢磨削烧伤表面的形貌 205
5.3.2 超高强度钢磨削烧伤表面酸洗后的形貌 207
5.3.3 超高强度钢磨削烧伤层的金相分析 209
5.3.4 超高强度钢磨削烧伤的巴克豪森噪声检测 211
5.4 超高强度钢磨削表面完整性 212
5.4.1 超高强度钢磨削表面粗糙度 212
5.4.2 超高强度钢磨削表层的显微硬度变化 214
5.4.3 超高强度钢磨削表层的残余应力 216
5.4.4 超高强度钢磨削表面完整性对疲劳强度的影响 221
5.5 超高强度钢低应力无烧伤磨削的措施 224
5.6 磨削超高强度钢的砂轮参数及磨削加工用量的选择 226
5.6.1 砂轮的选择原则 226
5.6.2 磨削加工用量的选择原则 227
5.6.3 磨削加工用量和砂轮参数的选择 227
第6章 不锈钢的磨削 233
6.1 不锈钢的材料特性及磨削特点 233
6.1.1 不锈钢的材料特性 233
6.1.2 不锈钢的磨削特点 234
6.2 磨削不锈钢的砂轮磨损 235
6.2.1 砂轮磨损特征 235
6.2.2 砂轮磨损率 239
6.3 磨削不锈钢的磨削力 242
6.3.1 砂轮黏附条件下的磨削力数学模型 242
6.3.2 砂轮磨损类型Ⅰ的磨削力 245
6.3.3 砂轮磨损类型Ⅱ的磨削力 246
6.3.4 砂轮磨损类型Ⅲ的磨削力 246
6.4 不锈钢磨削表面完整性 249
6.4.1 磨削加工硬化和残余应力 249
6.4.2 不锈钢的磨削烧伤 250
6.4.3 不锈钢的磨削划伤 253
6.5 磨削不锈钢的砂轮参数及磨削加工用量的选择 260
6.5.1 砂轮的选择原则 260
6.5.2 磨削加工用量的选择原则 263
6.5.3 磨削加工用量和砂轮参数的选择 264
第7章 典型工程陶瓷的磨削 275
7.1 典型工程陶瓷的性能及磨削特点 275
7.1.1 典型工程陶瓷的组成与显微结构 275
7.1.2 典型工程陶瓷的性能及用途 279
7.1.3 典型工程陶瓷的磨削特点 282
7.2 典型工程陶瓷的磨削过程及磨削表面微观形貌 283
7.2.1 超硬磨料砂轮及其修整 283
7.2.2 工程陶瓷磨削的材料去除机理及磨削表面的形成 288
7.2.3 典型工程陶瓷磨削表面的微观形貌 293
7.3 典型工程陶瓷的磨削力 298
7.3.1 工程陶瓷磨削力的理论计算 298
7.3.2 陶瓷磨削力的经验计算式 302
7.3.3 陶瓷磨削力的频谱分析 303
7.3.4 陶瓷磨削力的特点 306
7.3.5 影响陶瓷磨削力的因素 308
7.4 典型工程陶瓷的磨削温度 310
7.4.1 工程陶瓷磨削温度的理论分析 311
7.4.2 工程陶瓷磨削温度的测量 314
7.4.3 磨削条件对工程陶瓷磨削温度的影响 318
7.4.4 工程陶瓷磨削温度的经验计算式 320
7.5 典型工程陶瓷磨削工艺参数的选取 321
7.5.1 砂轮性能参数 321
7.5.2 磨削加工用量 325
7.5.3 其他磨削条件的选择 330
7.6 典型工程陶瓷的磨削新工艺 331
7.6.1 工程陶瓷的高效深切磨削技术 331
7.6.2 工程陶瓷的定压力磨削法 332
7.6.3 工程陶瓷的镜面磨削法 333
7.6.4 工程陶瓷的超声振动磨削技术 338
第8章 单晶硅片的磨削 342
8.1 单晶硅的材料特性及磨削特点 343
8.1.1 单晶硅的材料特性 343
8.1.2 单晶硅片的磨削特点 345
8.2 单晶硅片的磨削技术 346
8.2.1 转台式磨削 346
8.2.2 硅片旋转磨削 347
8.2.3 双面磨削 348
8.3 硅片的超精密磨削机理 349
8.3.1 超精密磨削硅片的材料去除机理 349
8.3.2 超精密磨削硅片表面的形成机理 355
8.4 硅片磨削表面完整性 362
8.4.1 磨削试验条件 363
8.4.2 磨削硅片的表面微观形貌和损伤 363
8.4.3 磨削硅片的亚表面损伤 365
8.5 硅片的磨削工艺参数的选择 377
8.5.1 工艺试验条件 377
8.5.2 工艺参数对磨削过程的影响及其选择 378
参考文献 381
- 《难加工材料磨削技术》任敬心,康仁科,王西彬编著 2011
- 《超硬与难磨削材料加工技术实例》辛志杰等编著 2013
- 《难加工材料的磨削》任敬心等编著 1999
- 《磨削技术经验》郑文虎编著 2014
- 《超声振动辅助磨削加工机理及理论研究》张洪丽著 2018
- 《现代磨削技术》李伯民,赵波主编 2003
- 《磨削原理》任敬心,华定安主编 2011
- 《磨削加工技术》庄司克雄编著 2007
- 《磨削加工技术》 2222
- 《磨削加工与磨具选择》池震宇编著 1990
- 《难加工材料磨削技术》任敬心,康仁科,王西彬编著 2011
- 《难加工材料的磨削》任敬心等编著 1999
- 《齿轮工程学》任敬心,刘洪忠等编著 1985
- 《磨削原理》任敬心,华定安主编 1988
- 《磨削原理》任敬心,华定安主编 2011
- 《金属零件可加工性技术》王西彬,龙振海等编 2009
- 《精密制造工学基础》王西彬,焦黎,周天丰编著 2018
- 《VRay效果图制作完全手册》任敬虎编著 2007
- 《中国开发区导论》任敬喜著 2000
- 《20世纪美国文学史》杨任敬著 1999
- 《北京工业志 电子志》卜世成,高玉庆主编 2001
- 《北京志 工业卷 68 电子工业志 仪器仪表工业志》北京市地方志编纂委员会编著 2001
- 《网络互联技术手册 第2版》(美)(K.唐斯)Kevin Downes等著;包晓露等译 1999
- 《当代北京广播电视和电子元件工业》《当代北京工业丛书》编辑部编 1988
- 《电子电路实验》梅开乡,梅军进主编;陈大力,吴勇平,李鹏鹏副主编 2014
- 《操作系统》韩仲清主编 1990
- 《'94北京国际电子出版研讨会论文集》粟武宾主编 1994
- 《dBASE Ⅲ PLUS》GOTOP编著 1995
- 《PowerPoint 97 操作导引》王耆,李文润编著 1998
- 《多媒体数据压缩技术》高文著 1994