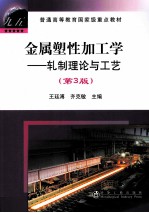
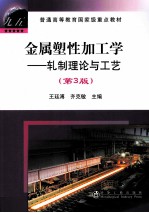
金属塑性加工学 轧制理论与工艺PDF格式文档图书下载
绪论 1
第一篇 轧制理论 5
1 轧制过程基本概念 5
1.1 变形区主要参数 5
1.1.1 轧制变形区及其主要参数 5
1.1.2 轧制变形的表示方法 8
1.2 金属在变形区内的流动规律 9
1.2.1 沿轧件断面高向上变形的分布 9
1.2.2 沿轧件宽度方向上的流动规律 12
2 实现轧制过程的条件 13
2.1 咬入条件 13
2.2 稳定轧制条件 15
2.3 咬入阶段与稳定轧制阶段咬入条件的比较 16
2.3.1 合力作用点位置或系数Kx的影响 16
2.3.2 摩擦系数变化的影响 16
2.4 改善咬入条件的途径 17
2.4.1 降低α角 17
2.4.2 提高β的方法 18
3 轧制过程中的横变形——宽展 19
3.1 宽展及其分类 19
3.1.1 宽展及其实际意义 19
3.1.2 宽展分类 19
3.1.3 宽展的组成 21
3.2 影响宽展的因素 22
3.2.1 影响轧件变形的基本因素分析 23
3.2.2 各种因素对轧件宽展的影响 27
3.3 宽展计算公式 31
3.3.1 А.И.采利柯夫公式 31
3.3.2 Б.П.巴赫契诺夫公式 32
3.3.3 S.爱克伦得公式 33
3.3.4 С.И.古布金公式 33
3.4 在孔型中轧制时宽展特点及其简化计算方法 34
3.4.1 在孔型中轧制时宽展特点 34
3.4.2 在孔型中轧制时计算宽展的简化方法 36
4 轧制过程中的纵变形——前滑和后滑 37
4.1 轧制过程中的前滑和后滑现象 37
4.2 轧件在变形区内各不同断面上的运动速度 38
4.3 中性角γ的确定 40
4.4 前滑的计算公式 42
4.5 影响前滑的因素 43
4.5.1 压下率对前滑的影响 43
4.5.2 轧件厚度对前滑的影响 43
4.5.3 轧件宽度对前滑的影响 44
4.5.4 轧辊直径对前滑的影响 44
4.5.5 摩擦系数对前滑的影响 44
4.5.6 张力对前滑的影响 45
4.6 连续轧制中的前滑及有关工艺参数的确定 45
4.6.1 连轧关系和连轧常数 46
4.6.2 前滑系数和前滑值 47
4.6.3 堆拉系数和堆拉率 48
5轧制压力及力矩的计算 50
5.1 计算轧制单位压力的理论 50
5.1.1 沿接触弧单位压力的分布规律 50
5.1.2 计算单位压力的Т.卡尔曼微分方程 50
5.1.3 单位压力卡尔曼微分方程的А.И.采利柯夫解 53
5.1.4 E.奥罗万单位压力微分方程和R.B.西姆斯单位压力公式 56
5.1.5 M.D.斯通单位压力微分方程式及其单位压力公式 58
5.2 轧制压力的工程计算 58
5.2.1 影响轧件对轧辊总压力的因素 58
5.2.2 接触面积的确定 60
5.2.3 金属实际变形抗力σ?的确定 62
5.2.4 平均单位压力的计算 66
5.2.5 常用数学模型举例 76
5.3 主电动机传动轧辊所需力矩及功率 78
5.3.1 传动力矩的组成 78
5.3.2 轧制力矩的确定 79
5.3.3 附加摩擦力矩的确定 81
5.3.4 空转力矩的确定 82
5.3.5 静负荷图 83
5.3.6 可逆式轧机的负荷图 83
5.3.7 主电动机的功率计算 85
6 不对称轧制理论 87
6.1 异步轧制理论 87
6.1.1 异步轧制基本概念及变形区特征 87
6.1.2 异步轧制压力 88
6.1.3 异步轧制的变形量及轧薄能力 90
6.1.4 异步轧制的轧制精度 90
6.1.5 异步轧制的振动问题 92
6.1.6 异步轧制有关参数的选择 92
6.2 轧辊直径不对称(异径)轧制理论 92
6.2.1 概述 92
6.2.2 异径轧制原理与工艺特点 93
第一篇练习题 97
第二篇 轧制工艺基础 99
7 轧材种类及其生产工艺流程 99
7.1 轧材的种类 99
7.1.1 按不同材质分类 99
7.1.2 按不同断面形状分类 100
7.2 轧材生产系统及生产工艺流程 101
7.2.1 钢材生产系统 101
7.2.2 碳素钢材的生产工艺流程 104
7.2.3 合金钢材的生产工艺流程 104
7.2.4 钢材的冷加工生产工艺流程 104
7.2.5 有色金属(铜、铝等)及其合金轧材生产系统及工艺流程 104
8 轧制生产工艺过程及其制订 107
8.1 轧材产品标准和技术要求 107
8.2 金属与合金的加工特性 108
8.2.1 塑性 108
8.2.2 变形抗力 109
8.2.3 导热系数 109
8.2.4 摩擦系数 109
8.2.5 相图形态 110
8.2.6 淬硬性 110
8.2.7 对某些缺陷的敏感性 110
8.3 轧材生产各基本工序及其对产品质量的影响 111
8.3.1 原料的选择及准备 111
8.3.2 原料的加热 112
8.3.3 钢的轧制 115
8.3.4 钢材的轧后冷却与精整 118
8.3.5 钢材质量的检查 118
8.4 制订轧制产品生产工艺过程举例 119
8.4.1 制订轧钢产品生产工艺过程举例 119
8.4.2 制订有色金属轧材生产工艺过程举例 120
9 轧材生产新工艺及其技术基础 122
9.1 连续铸造及其与轧制的衔接工艺 122
9.1.1 连续铸钢技术 122
9.1.2 连铸坯液芯软压下技术 125
9.1.3 连铸与轧制的衔接工艺 127
9.2 控制轧制与控制冷却基础 136
9.2.1 钢材的强化机制 137
9.2.2 钢材热变形过程中的再结晶和相变行为 140
9.2.3 钢材的控制轧制 144
9.2.4 钢材轧后控制冷却及直接淬火工艺 146
第二篇练习题 150
第三篇 型材和棒线材生产 152
10 大、中型型材及复杂断面型材生产 152
10.1 生产特点、用途及典型产品 152
10.1.1 型材的生产特点 152
10.1.2 型材的分类、用途及市场对型材的要求 152
10.1.3 典型产品 154
10.2 轧机规格、轧制工艺和轧机布置 159
10.2.1 轧机命名原则、轧机尺寸和轧机形式 159
10.2.2 型材轧制工艺 160
10.2.3 型材轧机的典型布置形式 162
10.3 二辊孔型与四辊万能孔型轧制凸缘型钢的区别 164
10.3.1 凸缘型钢的轧制特点及使用万能孔型轧制凸缘型钢的优点 164
10.3.2 轧件在万能孔型和轧边端孔型中的变形特点 165
10.3.3 横列式轧机与两辊开坯机接万能轧机轧制凸缘型钢的区别 167
10.3.4 轧制重轨时万能孔型的作用分析 167
10.4 初轧开坯生产的历史、现状及改造方向 169
10.4.1 初轧生产的历史和现状 169
10.4.2 初轧机的类型及生产特点 170
10.4.3 初轧生产工艺 171
10.4.4 我国初轧机的前景和可能的改造方案 173
10.5 三辊中型型钢轧机在我国的现状及改造的设想 174
10.5.1 我国中型型钢轧机及生产简况 174
10.5.2 改造中型型钢轧机的必备条件 175
10.5.3 中型型钢轧机的改造方案 175
10.6 大、中型型钢生产新技术 176
10.6.1 连铸异型坯及连铸坯直接热装轧制(CC-DHCR) 176
10.6.2 在线控轧控冷和余热淬火 177
10.6.3 长尺冷却和长尺矫直 177
10.6.4 机械工程用钢 177
10.6.5 热弯型钢 178
10.6.6 H型钢生产新技术 178
11 棒、线材生产 179
11.1 棒、线材的种类和用途 179
11.1.1 棒、线材的种类和用途 179
11.1.2 市场对棒、线材的质量要求 180
11.2 棒、线材的生产特点和生产工艺 180
11.2.1 棒、线材的生产特点 180
11.2.2 棒、线材的生产工艺 181
11.3 棒、线材轧制的发展方向 182
11.3.1 连铸坯热装热送或连铸直接轧制 182
11.3.2 柔性轧制技术 183
11.3.3 高精度轧制 183
11.3.4 继续提高轧制速度 183
11.3.5 低温轧制 183
11.3.6 无头轧制 184
11.3.7 切分轧制 185
11.4 棒、线材轧机的布置形式 185
11.4.1 棒、线材轧机的发展过程 185
11.4.2 现代化棒、线材轧机 187
11.5 棒、线材轧制的控制冷却和余热淬火 192
11.5.1 概述 192
11.5.2 螺纹钢筋轧后余热淬火处理工艺的特点及其原理 192
11.5.3 线材控制冷却的基本原理 193
11.5.4 线材控制冷却方法简介 194
12 型材和棒、线材轧制及其轧制过程的自动化控制 196
12.1 轧制方法、轧制条件和变形特点 196
12.1.1 轧制特征和轧制方法 196
12.1.2 轧制变形参数 197
12.1.3 咬入条件 198
12.1.4 延伸与宽展 199
12.1.5 在轧槽内轧件的变形 200
12.1.6 前滑和后滑 202
12.1.7 型材轧制的孔型系统举例 202
12.2 在孔型中轧件变形的数值模拟 206
12.3 连轧的张力特性及张力控制 207
12.3.1 棒、线材连轧的机架间张力特性 207
12.3.2 棒、线材连轧的张力控制 208
12.3.3 型材轧制的张力特性及张力控制 209
12.4 型材和棒、线材轧制的自动控制 210
12.4.1 型材和棒、线材的尺寸自动测量 210
12.4.2 轧件尺寸自动控制 210
12.4.3 型材和棒、线材轧制的计算机控制 211
第三篇练习题 213
第四篇 板、带材生产 215
13 板、带材生产概述 215
13.1 板、带产品特点、分类及技术要求 215
13.1.1 板、带产品的外形、使用与生产特点 215
13.1.2 板、带材的分类及技术要求 216
13.2 板、带轧制技术的辩证发展 217
13.2.1 围绕降低金属变形抗力(内阻)的演变与发展 217
13.2.2 围绕降低应力状态影响系数(外阻)的演变与发展 219
13.2.3 围绕减少和控制轧机变形的演变与发展 222
14 热轧板、带材生产 224
14.1 中、厚板生产 224
14.1.1 中、厚板轧机的型式及其布置 224
14.1.2 中、厚板生产工艺 225
14.2 热连轧带钢生产 230
14.2.1 原料选择与加热 232
14.2.2 粗轧 232
14.2.3 精轧 236
14.2.4 调宽轧制(AWC)及自由程序轧制(SFR) 239
14.2.5 轧后冷却及卷取 242
14.2.6 热带连轧机工艺流程与车间布置 243
14.2.7 厚板坯连铸连轧(DHCR+DR)工艺流程与车间布置 244
14.3 中小型企业薄板带钢生产 246
14.3.1 叠轧薄板生产 247
14.3.2 炉卷轧机热轧带钢生产 247
14.3.3 行星轧机热轧带钢生产 249
14.4 薄(中厚)板带坯连铸连轧及薄带铸轧技术 252
14.4.1 概述 252
14.4.2 几种薄板坯连铸连轧工艺技术及其比较 253
14.4.3 轧材的组织性能特点 256
14.4.4 薄板坯无头高速连铸连轧(ESP)技术的新发展 257
14.4.5 薄(中)板坯连铸连轧(TSCR)技术的发展趋势 258
14.4.6 薄带连续铸轧技术 259
15 冷轧板、带材生产 262
15.1 冷轧板、带材生产工艺特点 262
15.1.1 加工温度低,在轧制中将产生不同程度的加工硬化 262
15.1.2 冷轧中要采用工艺冷却和润滑 262
15.1.3 冷轧中要采用张力轧制 265
15.2 冷轧板、带材生产工艺流程 267
15.2.1 冷轧板、带材的主要品种、工艺流程与车间布置 267
15.2.2 原料板卷的酸洗与除鳞 268
15.2.3 冷轧 270
15.2.4 冷轧板、带钢的精整 274
15.3 极薄带材生产 275
15.3.1 关于轧机最小可轧厚度问题 275
15.3.2 极薄带材轧制的特点 276
15.3.3 极薄带材轧制生产工艺 276
16 板、带材高精度轧制和板形控制 278
16.1 板、带材轧制中的厚度控制 278
16.1.1 P-h图的建立与运用 278
16.1.2 板、带材厚度变化的原因和特点 279
16.1.3 板、带材厚度控制方法 280
16.2 横向厚差与板形控制技术 282
16.2.1 板形与横向厚差的关系 282
16.2.2 影响辊缝形状的因素 287
16.2.3 轧辊辊型设计 289
16.2.4 辊型及板形控制技术 291
17 板、带材轧制制度的确定 303
17.1 制定轧制制度的原则和要求 303
17.1.1 在设备能力允许的条件下尽量提高产量 303
17.1.2 在保证操作稳便的条件下提高质量 305
17.2 压下规程或轧制规程设计(设定) 307
17.2.1 概述 307
17.2.2 中、厚板轧机压下规程设计 308
17.2.3 热连轧板、带钢轧制规程设定 313
17.2.4 冷轧板、带钢轧制规程制定 323
第四篇练习题 327
第五篇 管材生产工艺和理论 331
18 热轧无缝管材的主要加工形式和基本工艺过程 331
18.1 穿孔方法 331
18.1.1 斜轧穿孔 331
18.1.2 压力挤孔 333
18.2 轧管方法 333
18.2.1 自动轧管机 333
18.2.2 连续轧管机 334
18.2.3 高精度轧管机 337
18.2.4 顶管机 338
18.2.5 周期轧管机 338
18.2.6 管材热挤压 339
18.3 毛管精轧 340
18.3.1 减径机 340
18.3.2 定径机 340
18.4 热轧无缝钢管生产的一般工艺过程 340
19 斜轧原理与工具设计 344
19.1 斜轧过程的运动学 344
19.2 斜轧过程中轧件的变形 348
19.2.1 变形计算 348
19.2.2 变形特点分析 349
19.3 斜轧的曳入条件 355
19.3.1 第一次曳入条件 356
19.3.2 第二次曳入条件 356
19.4 斜轧穿孔压力和力矩的计算 359
19.4.1 斜轧穿孔压力的计算 359
19.4.2 斜轧穿孔力矩的计算 359
19.5 斜轧穿孔机的工具设计 361
19.5.1 穿孔机轧辊设计 361
19.5.2 斜轧穿孔的顶头设计 362
19.5.3 斜轧穿孔的导向装置设计 363
20 管材纵轧原理和工具设计 366
20.1 管材纵轧变形区的特点 366
20.2 管材纵轧变形区的速度分析 368
20.3 管材纵轧的咬入条件 370
20.4 管材纵轧的轧制力和轧制力矩 371
20.4.1 接触表面水平投影面积计算 371
20.4.2 平均单位压力、芯棒轴向力计算 373
20.4.3 管材纵轧的力矩计算 375
20.5 纵轧管机的工具设计和轧机调整 376
20.5.1 自动轧管机 376
20.5.2 连续轧管机 378
20.5.3 减径机 386
20.6 轧制表计算 393
20.6.1 轧制表的作用 393
20.6.2 连续轧管机组的轧制表计算举例 393
21 管材冷加工 398
21.1 管材冷加工概述 398
21.1.1 管材冷拔的主要方法 398
21.1.2 管材冷轧的主要方法 399
21.2 周期式冷轧管机轧制的变形原理和工具设计 402
21.2.1 周期式冷轧管机的轧制过程 402
21.2.2 变形区内金属的应力状态分布 403
21.2.3 周期轧制中各主要变形参数的计算 406
21.2.4 二辊式周期冷轧管机的孔型设计 408
21.2.5 周期式冷轧管机的作用力 413
22 焊管生产工艺 416
22.1 电焊管生产方法概述 416
22.1.1 辊式连续成型机生产电焊管 416
22.1.2 履带式成型机生产电焊管 417
22.1.3 几种大口径钢管的生产方法 417
22.2 辊式连续成型机生产电焊钢管的基本问题 419
22.2.1 机架的排列与布置 419
22.2.2 管坯成型的变形过程 419
22.2.3 成型底线 420
22.2.4 薄壁管成型 421
22.2.5 厚壁钢管生产 423
22.3 辊式连续成型机的轧辊孔型设计 424
22.3.1 带钢边缘弯曲法 424
22.3.2 带钢圆周弯曲法 425
22.3.3 带钢综合弯曲法 426
22.3.4 双面弯曲侧弯成型法 426
22.4 带钢综合弯曲法的孔型设计 427
22.4.1 带钢宽度的计算 427
22.4.2 挤压辊孔型计算 427
22.4.3 变形分配 428
22.4.4 设计计算各机架的孔型 428
22.4.5 立辊辊型计算 431
22.4.6 定径机轧辊孔型计算 433
22.4.7 矫直头孔型计算 433
第五篇练习题 434
参考文献 435
- 《金属塑性加工学 轧制理论与工艺 第2版》王廷溥,齐克敏主编 1998
- 《高等学校教学用书 金属塑性加工学-轧制理论与工艺》东北工学院,王廷溥 1988
- 《金属塑性加工学 轧制理论与工艺》王廷溥,齐克敏主编 2012
- 《金属塑性变形与轧制理论》赵志业编 1980
- 《金属塑性加工 轧制理论与工艺》王廷溥主编 1988
- 《金属塑性变形与轧制理论 第2版》赵志业主编 1980
- 《轧制工程学》贺毓辛编著 2010
- 《塑性变形与轧制原理》袁志学,王淑平主编 2008
- 《塑性变形与轧制原理》黄守汉主编 1991
- 《塑性变形力学基础与轧制原理》曹鸿德编 1981
- 《工业管道泄漏防治》阮徐狓,仉家骅编 1988
- 《网络互联技术手册 第2版》(美)(K.唐斯)Kevin Downes等著;包晓露等译 1999
- 《俄汉工业产权词汇》中国专利局信息中心编译 1990
- 《俄语疑难姓氏词典》刘星华编 1994
- 《THE GOVERNMENT/PRESS CONNECTION PRESS OFFICERS AND THEIR OFFICES》STEPHEN HESS 1984
- 《魏寿昆传》吴石忠,姜曦编著 2011
- 《PRESS》POLITICS & PUBLIC OPINION IN BIHAR 1912-1947 2010
- 《Press law》Robin Callender Smith. 1978
- 《森林工业译丛 第5辑 采伐循环作业》中国林业出版社编 1956
- 《SUING THE PRESS》RODNEY A.SMOLLA 1986