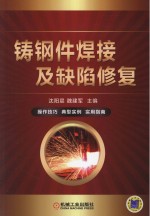
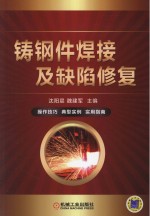
铸钢件焊接及缺陷修复PDF格式文档图书下载
- 购买点数:12 点
- 作 者:沈阳晨 魏建军主编 黄智泉 宁德林 杨晓兵 潘健副主编
- 出 版 社:北京:机械工业出版社
- 出版年份:2016
- ISBN:9787111516064
- 标注页数:339 页
- PDF页数:349 页
第1章 铸钢基础知识 1
1.1 铸钢的主要特点及分类 1
1.1.1 铸造碳钢 1
1.1.2 铸造低合金钢 2
1.1.3 铸造高合金钢 4
1.2 常用铸钢件材料分类 7
1.3 铸钢的特性 9
1.4 铸钢件常见缺陷及其产生原因 11
1.4.1 铸钢件的铸造缺陷分类 11
1.4.2 铸造缺陷产生原因分析 13
1.5 铸钢件的热处理 16
1.5.1 铸钢件热处理的目的 16
1.5.2 铸钢件热处理的主要方式 16
1.5.3 铸钢件的表面淬火 17
1.5.4 各种常用铸钢件的热处理 17
1.5.5 铸钢件焊接或补焊后预防白点退火与去应力处理 18
第2章 铸钢件的焊接 21
2.1 概述 21
2.2 铸钢件的焊接性 22
2.2.1 焊接性的定义 22
2.2.2 铸钢件的焊接性特点 22
2.2.3 焊缝热影响区宽度 23
2.3 常用铸钢材料的焊接性 23
2.3.1 铸造碳钢的焊接性 23
2.3.2 铬钼系及铬钼钒系耐热钢的焊接性 25
2.3.3 其他低合金钢的焊接性 25
2.3.4 低碳马氏体不锈钢的焊接性 26
2.3.5 ω(Cr)=9%~12%的超临界钢、超超临界和超高温钢的焊接性 26
2.3.6 奥氏体不锈钢铸钢的焊接性 29
2.3.7 铁素体-奥氏体双相不锈钢的焊接性 30
2.3.8 高锰钢的焊接性 31
2.3.9 低温用铸造低合金钢的焊接性 32
2.4 铸钢的组装焊接 33
2.4.1 铸钢与铸钢接合的焊接结构 33
2.4.2 铸钢与钢板制作的管道或锻钢管接头等的焊接 34
2.4.3 在钢板结构件上采用铸钢件 35
2.4.4 铸钢件组装焊接的特点 35
2.4.5 铸钢件组焊操作技巧 35
2.5 铸钢件焊接或补焊常用的焊接方法及适用性 37
2.5.1 焊条电弧焊 38
2.5.2 埋弧焊 39
2.5.3 气体保护焊 40
2.5.4 脉冲钨极氩弧焊技术 54
2.5.5 精密脉冲冷焊技术 56
2.5.6 常用焊接方法的适用性 57
2.6 焊接材料 59
2.6.1 焊接材料的选用原则 59
2.6.2 焊缝成分的控制 59
2.6.3 焊条的选择 60
2.6.4 气体保护焊实心焊丝的选择 61
2.6.5 铸钢件焊接或补焊焊缝的强度匹配 62
2.6.6 铸钢件补焊焊接材料消耗的计算方法 63
2.7 粘接(金属填补)技术 63
2.7.1 粘接技术基础 64
2.7.2 粘补工艺的一般过程 64
2.7.3 粘接技术在铸钢件缺陷修补中的应用 65
第3章 铸钢件缺陷的修补 67
3.1 铸钢件缺陷修补的意义 67
3.2 铸钢件缺陷修补的要求 67
3.3 铸钢件缺陷修补的可行性及可靠性 68
3.4 铸钢件缺陷修补的限制 68
3.4.1 主要缺陷的补焊规定 68
3.4.2 缺陷修补限制的必要性 69
3.4.3 限制修补的条件 69
3.5 铸造缺陷的焊接修补特点 70
3.6 铸钢件缺陷的焊接修补程序 70
3.7 铸钢件的缺肉堆焊 70
第4章 铸钢件焊接与补焊工艺规程的编制方法 73
4.1 概述 73
4.2 焊接与补焊工艺规程的文件形式 74
4.3 工艺规程的编写依据 75
4.4 工艺规程的编制方法 76
4.4.1 铸钢件的焊接工艺 76
4.4.2 铸钢件的缺陷补焊工艺 78
4.4.3 铸钢件焊接与补焊工艺规程的有效性 89
4.4.4 工艺规程的执行和工艺纪律检查 89
第5章 铸钢件焊接与补焊缺陷的防止措施及质量管理 91
5.1 铸钢件焊接与补焊的常见缺陷及防止措施 91
5.1.1 外观形状和尺寸不符合要求的产生原因及防止措施 92
5.1.2 裂纹的产生原因及防止措施 92
5.1.3 气孔的产生原因及防止措施 93
5.1.4 夹渣的产生原因及防止措施 95
5.1.5 未焊透与未熔合的产生原因及防止措施 96
5.1.6 色差及硬度不均匀的产生原因及防止措施 96
5.1.7 铸钢件补焊缺陷的产生原因及防止措施 97
5.2 铸钢件焊接与补焊质量管理 98
5.2.1 质量管理的基本概念 98
5.2.2 铸钢件焊接与补焊质量管理的控制环节 99
5.2.3 质量管理与焊接检验的关系 102
5.3 铸钢件的焊接工艺评定 102
5.3.1 焊接工艺评定的目的及影响因素 103
5.3.2 焊接工艺评定报告与焊接工艺规程的重要作用 104
5.3.3 焊接工艺评定的规则、程序及注意事项 105
5.4 焊接与补焊质量的控制及检验 107
5.5 铸钢件焊接与补焊质量的检查及验收标准 109
5.5.1 焊接技术标准 109
5.5.2 焊接与补焊质量的检查方法 110
5.5.3 铸钢件焊接或补焊区无损检测有关要求 110
5.5.4 补焊区硬度测试检验要求 111
5.6 影响铸钢件焊接与补焊质量的不规范操作 111
5.7 铸钢件焊接与补焊过程中错误的习惯认识 112
第6章 铸钢件的变形与矫正 119
6.1 铸钢件变形的特点 119
6.2 铸钢件变形的矫正 120
6.2.1 冷态矫正 120
6.2.2 局部加热加压矫正 121
6.2.3 火焰矫正 122
6.2.4 整体加热矫正 123
6.3 铸钢件矫正变形的常见缺陷及防止措施 123
6.4 不同材料铸钢件变形矫正的特点 124
6.4.1 马氏体不锈钢铸钢件变形矫正的特点 124
6.4.2 奥氏体不锈钢铸钢件焊接变形矫正的特点 125
6.4.3 碳素钢及一般合金钢铸钢件变形矫正的特点 125
6.5 厚大截面铸钢件变形的火焰局部矫正 125
6.5.1 火焰局部矫正的特点 125
6.5.2 火焰局部矫正的原理及方法 125
第7章 铸钢件焊接与补焊操作技巧 127
7.1 铸钢件焊接与补焊存在的主要问题 127
7.2 铸钢件严重疏松性缺陷的修复要点 130
7.2.1 缺陷的清除 130
7.2.2 坡口要求及处理 131
7.2.3 补焊修复操作要点 132
7.3 采用奥氏体不锈钢焊接材料焊接与补焊非奥氏体铸钢件的要点 133
7.4 铸钢件大(深)坡口的补焊操作技巧 134
7.4.1 存在的主要问题 134
7.4.2 缺陷原因分析 134
7.4.3 补焊操作技术及要求 135
7.4.4 修补后的去应力处理 137
7.5 坡口形状对铸钢件补焊质量的影响 138
7.5.1 铸钢补焊常用的未穿透性坡口形状 138
7.5.2 铸钢补焊常用的穿透性坡口形状 140
7.6 铸钢件完全精加工状态下的缺陷修复 140
7.7 焊接与补焊操作注意事项 142
第8章 常用铸钢材料的焊接与补焊 148
8.1 铸造碳钢 148
8.1.1 铸造碳钢的碳当量及焊接性 148
8.1.2 铸造碳钢的焊接或补焊特点 148
8.1.3 铸造碳钢的焊接或补焊要点 149
8.1.4 焊接方法与焊接材料 150
8.1.5 焊后去应力处理 150
8.2 铸造低合金钢 151
8.2.1 铸造低合金钢的碳当量与热处理类型 151
8.2.2 退火、正火+回火的铸钢件 152
8.2.3 调质处理的铸钢件 153
8.3 铬钼及铬钼钒耐热铸钢 156
8.3.1 铬钼及铬钼钒低合金耐热铸钢的焊接特点 156
8.3.2 对铬钼及铬钼钒耐热铸钢件焊接接头或补焊区的基本要求 157
8.3.3 铬钼及铬钼钒耐热铸钢的焊接与补焊要点 157
8.3.4 常用铬钼及铬钼钒耐热铸钢焊接材料的选用 158
8.3.5 焊后去应力热处理 158
8.4 低碳马氏体不锈钢 159
8.4.1 低碳马氏体不锈钢铸钢件的焊接特点 159
8.4.2 低碳马氏体不锈钢铸钢件的焊接与补焊要点 159
8.4.3 常用马氏体不锈钢焊接材料的选用 160
8.4.4 Ar+CO2富氩混合气体保护焊的应用 160
8.5 奥氏体不锈钢铸钢 161
8.5.1 奥氏体不锈钢铸钢件的焊接特点 161
8.5.2 奥氏体不锈钢铸钢件的焊接与补焊要点 161
8.5.3 常用奥氏体不锈钢铸件焊接材料的选用 162
8.6 双相不锈钢 162
8.6.1 Cr18型双相不锈钢的焊接要点 162
8.6.2 Cr25型双相不锈钢的焊接要点 162
8.6.3 Cr22型双相不锈钢的焊接要点 163
8.7 超(超)临界和超高温钢铸钢 163
8.7.1 焊接或补焊工艺特点 163
8.7.2 超(超)临界铸钢件补焊工艺要点 164
8.7.3 常用超(超)临界铸钢件焊接材料的选用 164
8.8 高锰钢铸件 164
8.8.1 高锰钢铸件的焊接特点 164
8.8.2 高锰钢铸件的焊接与补焊要点 165
8.8.3 常用高锰钢铸件焊接材料的选用 165
8.9 低温铸钢件的焊接与补焊要点 165
第9章 设备在线焊接修复实例 167
9.1 M16T锤砧座的焊接修复 167
9.2 DLA180机床主轴的堆焊修复 170
9.3 上梁裂纹的焊接修复 171
9.4 120MN水压机活动横梁断裂焊接修复 173
9.5 水压机底座裂纹的焊接修复 177
9.6 水压机主缸衬套裂纹的焊接修复 179
9.7 转炉耳轴支块裂纹的在线焊接修复 181
9.8 ZG270-500三联液压缸缸体的焊接修复 185
9.9 ZG270-500三联液压缸缸体的冷焊修复 186
9.10 热模锻压力机机架的焊接修复 188
9.11 热模锻压力机机架焊接修复工艺评定试验 193
第10章 铸钢件产品缺陷焊接修复实例 199
10.1 低碳马氏体不锈钢铸钢件的焊接修复 200
10.1.1 叶片缺陷的焊接修复 200
10.1.2 水轮机上冠的焊接修复 206
10.1.3 水轮机下环的焊接修复 212
10.1.4 水轮机导叶的焊接修复 215
10.1.5 水电、风电铸钢件产品缺陷的焊接修复 218
10.2 铰座、铰链的焊接修复 226
10.2.1 铰座的焊接修复 226
10.2.2 铰链加工失误的补焊修复 230
10.3 轧机铸钢件产品的焊接修复 232
10.3.1 支承辊轴承座的焊接修复 232
10.3.2 工作辊轴承座缺陷的补焊修复 235
10.3.3 轧机牌坊(机架)的补焊修复 238
10.3.4 立辊机架的焊接修复 250
10.4 火电气缸铸钢件缺陷的焊接修复 254
10.4.1 气缸缺陷的焊接修复 254
10.4.2 高压外缸缺陷的补焊修复 264
10.4.3 气缸缺陷的焊接修复 273
10.5 火电阀壳、阀体、导流环等的缺陷焊接修复 277
10.6 锻压设备铸钢件缺陷的焊接修复 281
10.6.1 模锻锤下锤头缺陷的焊接修复 281
10.6.2 快锻压机铸钢件缺陷的焊接修复 282
10.6.3 热模锻压力机铸钢件缺陷的焊接修复 285
10.6.4 活动横梁下垫板裂纹的焊接修复 289
10.6.5 侧梁下部裂纹缺陷的焊接修复 290
10.7 工作台缺陷的补焊修复 291
10.8 齿圈、齿轮缺陷的补焊修复 294
10.9 其他铸钢件缺陷的焊接修复 297
10.10 环形铸钢件变形的矫正与修复 315
10.10.1 大型整铸环型铸钢件变形的火焰热矫 316
10.10.2 大型整铸环型铸钢件变形的加压火焰热矫 317
第11章 铸钢件组焊或接管等构件的焊接 319
11.1 挖斗体与斗唇、磨损套、中间套的装焊 319
11.2 高压外缸排气管的焊接 321
11.3 转轮体不锈钢堆焊及肋板的焊接 323
11.4 球体与面板的组焊 326
11.5 塔柱封板的装焊 328
11.6 高压外缸与钢管的焊接 330
11.7 中压排气缸构件的焊接 332
11.8 高压主气阀阀壳进气连管的组焊 333
11.9 高压外缸构件的装焊 335
参考文献 339
- 《铸钢件焊接及缺陷修复》沈阳晨,魏建军主编;黄智泉,宁德林,杨晓兵,潘健副主编 2016
- 《铸钢铸铁焊接要点》(日)副岛一雄,(日)仁熊贤次著;张锐译 1980
- 《铸钢·铸铁焊接的重点》焊接丛书编辑委员会编;刘荣宗译 1977
- 《铸钢表面缺陷的防止方法》日本铸造协会铸钢表面缺陷研究委员会编写;吴炳荣译 1984
- 《现代焊接生产手册》上海市焊接协会编 2007
- 《汽车车身修复》翟大锋主编;张举全,张志俊副主编 2016
- 《焊接技术经验》李淑华,郑鹏翱编著 2014
- 《大型火电机组检修实用技术丛书 金属与焊接分册》郭延秋主编 2003
- 《电站金属实用焊接技术》许江晓编著 2011
- 《铸钢件生产指南》沈阳市铸造协会组织编写 2008
- 《铸钢件焊接及缺陷修复》沈阳晨,魏建军主编;黄智泉,宁德林,杨晓兵,潘健副主编 2016
- 《焊接材料手册》龙伟民,陈永主编;魏建军,钟素娟,黄智泉副主编 2014
- 《焊接工程质量评定方法及检测技术》龙伟民,刘胜新主编;黄智泉,陈永副主编;杨威,李军伟,张海燕,张永生,尼军杰,苗晋琦,夏静,鲁科明,孙玉福,卢广玺,王乐军,李杏瑞,潘继民,杨晗,马超宁参编 2015
- 《矿山机械》魏大恩主编;杨晓明,陈国山,郑建军,杨明春副主编 2017
- 《糖尿病防治 绘画本》顾沈兵主编;高晶蓉,胡兆铭,丁园副主编;魏晓敏,陈德,杨建军等编;蔡康非绘画 2015
- 《河南省畜禽疫病志》河南省畜牧局编;王淑如主编;吴德林,舒敬业,魏永顺副主编 1993
- 《金属材料常识普及读本》陈永主编;徐军福,李国立,冯纪东,黄智泉副主编;徐向俊,潘继民,李军伟,张永生,尼军杰,杨威,赵轩玮,蒋思涵,孙为云,霍方方,翟德铭,陈光,李书珍,王朋旭,王鸿杰参编 2016
- 《高分子导论》姚天扬,孙尔康总主编;陆云,左晓兵主编;董锐,孙幼红,章峻副主编;宁春花,朱亚辉,薛春彦,薛爱莲参编;余学海主审 2014
- 《OCT血流成像图谱》魏文斌主编;杨文利,杨丽红,史雪辉副主编;丁宁,王红,王子杨,史雪辉,李栋军,李逸丰,杨文利,杨丽红,沈琳,陈伟,赵琦,唐炘,崔蕊,魏文斌,RUIKANGK.WANG编 2016
- 《金属工艺学 第2版》李长河,杨建军主编;刘琨明,杨发展,张霞,胡耀增副主编 2018
- 《北京志 工业卷 机械工业志 农机工业志》北京市地方志编纂委员会编 2001
- 《机械工业和机械图书的出版发行 机械工业出版社发行培训教材》陈慧毅,杨少晨编 1988
- 《冷冲模设计》赵孟栋主编 2006
- 《机械工业出版社》慕拉维叶夫著;孔庆复译 1959
- 《北京市立高级工业职业学校机械科毕业学生韩丕纯分数表/韩丕纯毕业证书》 1949
- 《中等职业教育机电类规划教材 机械工业出版社精品教材 机械设计基础 第2版》机械职业教育基础课教学指导委员会机械设计学科组组编;柴鹏飞主编 2006
- 《集知播识春秋录 机械工业出版社 1952-1988.机械科学技术情报研究所 1958-1988》机械科技情报研究所,机械工业出版社编 1988
- 《电线电缆》上海市电缆研究所编 1975
- 《FoxBASE+ 三周通》文忠等编著 1995
- 《FoxBASE+实验指导书》李爱华,王建诚编 1994