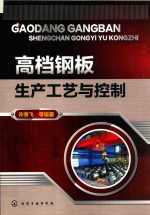
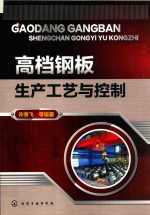
高档钢板生产工艺与控制PDF格式文档图书下载
- 购买点数:11 点
- 作 者:许秀飞等编著
- 出 版 社:北京:化学工业出版社
- 出版年份:2018
- ISBN:9787122316257
- 标注页数:278 页
- PDF页数:295 页
第一章 常见各钢种生产工艺 1
第一节 铝镇静钢及其生产工艺 1
1.什么是低碳钢和微碳钢的时效性? 1
2.时效性产生的根本原因是什么? 2
3.时效性与产品含碳量有什么关系? 2
4.时效性与基体固溶碳含量有什么关系? 3
5.低碳、微碳钢在退火加热时组织发生什么转变? 4
6.微碳钢在退火加热时的组织转变有什么特点? 4
7.低碳钢在退火加热时的组织转变有什么特点? 5
8.低碳、微碳钢在连续退火保温时发生什么转变? 7
9.低碳、微碳钢在连续退火冷却时发生什么转变? 7
10.低碳、微碳钢在连续退火过时效阶段发生什么转变? 8
11.低碳、微碳钢的组织对力学性能有什么影响? 8
12.铝镇静钢常见元素各起什么作用? 9
13.化学成分对铝镇静钢的性能有何影响? 9
14.碳、锰含量对低碳钢的性能有什么影响? 10
15.如何选择铝镇静钢的化学成分? 11
16.理论上过时效处理温度有什么影响? 11
17.连续退火工艺对产品性能有什么影响? 12
18.快冷速度和过时效工艺对产品性能的影响? 15
19.快冷速度和过时效温度对渗碳体形态的影响? 16
20.快冷速度和过时效温度对渗碳体间距的影响? 17
21.快冷速度是怎样影响晶粒内部固溶碳分布的? 18
22.晶粒内部固溶碳分布的量化计算有什么结果? 19
23.终冷后最大固溶碳的量化计算有什么结果? 19
24.热镀锌生产工艺对产品性能有何影响? 20
第二节 镀锡基板生产工艺 21
25.镀锡基板有何特点? 21
26.镀锡基板的钢种如何分类? 22
27.镀锡基板的化学成分有什么要求? 22
28.镀锡基板的调质度如何分级? 22
29.不同调质度产品的生产工艺有何不同? 23
30.镀锡基板化学成分选择的原则是什么? 24
31.如何选择镀锡基板的含碳量? 24
32.镀锡基板加铌的原理如何? 24
33.镀锡基板加氮的原理如何? 24
34.如何采用连退生产所有调质度的镀锡基板? 25
35.如何采用连退生产T-1级镀锡板? 26
36.镀锡基板对炼钢有何要求? 26
37.镀锡基板对连铸有何要求? 26
38.镀锡基板对轧制有什么要求? 27
第三节 无间隙原子钢及其生产工艺 27
39.什么是无间隙原子钢? 27
40.Ti-IF钢和Nb-IF钢的性能有什么差异? 27
41.Ti-IF钢和Nb-IF钢的组织有什么差异? 28
42.(Ti+Nb)-IF钢有什么特点? 28
43.IF钢的生产工艺有什么特点? 29
44.如何选择IF钢的合金元素含量? 30
45.如何选择IF钢的含碳量? 30
46.IF钢有哪几种冶炼工艺路线? 32
47.IF钢的冶炼工艺有什么要点? 32
48.IF钢的热轧工艺有什么要点? 33
49.IF钢的冷轧工艺有什么要点? 34
50.IF钢的退火工艺有什么要点? 34
51.如何确定(Ti+Nb)-IF钢的退火工艺? 35
第四节 传统高强钢及其生产工艺 35
52.钢材常见的强化途径有哪些? 36
53.汽车板生产中常用哪些强化方法? 36
54.高强度低合金钢有什么特点? 37
55.磷强化低合金钢有什么特点? 38
56.如何确定高强度低合金钢的生产工艺? 39
57.高强IF钢有什么特点? 39
58.在高强IF钢中常加入哪些合金元素? 40
59.不同合金元素对高强IF钢的性能有什么作用? 40
60.如何选择高强IF钢的化学成分? 41
61.如何确定高强IF钢的生产工艺? 42
62.烘烤硬化钢有何特点? 43
63.如何选择BH钢的化学成分? 44
64.BH钢的生产工艺有何特点? 44
65.BH钢的退火工艺与性能有什么关系? 45
第五节 先进高强钢及其生产工艺 47
66.什么是先进高强钢? 47
67.冷轧薄板常见哪些组织? 48
68.常见组织的性能有什么特点? 49
69.什么是过冷奥氏体转变的TTT曲线? 50
70.过冷奥氏体等温状态发生哪些转变? 51
71.什么是过冷奥氏体的CCT曲线? 51
72.怎样通过调整冷却路线来改变组织的性能? 53
73.什么是DP钢、FB钢和CP钢? 53
74.DP钢的组织有什么特点? 54
75.DP钢的性能有什么特点? 55
76.DP钢化学成分有什么特点? 55
77.DP钢对热轧和冷轧工艺有什么要求? 56
78.DP钢对连续退火工艺有什么要求? 56
79.如何选择DP钢的连续退火工艺参数? 57
80.什么是TRIP钢? 58
81.TRIP钢的组织有什么特征? 59
82.TRIP钢各种组织分别起什么作用? 60
83.TRIP钢的性能有什么特点? 62
84.TRIP钢的化学成分对性能有什么影响? 62
85.TRIP钢轧钢工艺有什么要求? 63
86.TRIP钢连续退火工艺有何特点? 63
87.什么是TWIP钢? 65
88.TWIP钢的组织和性能有什么特点? 66
89.TWIP钢的化学成分有什么特点? 68
90.什么是马氏体高强钢(Ms钢)? 69
91.淬火过程的马氏体转变有什么特点? 69
92.马氏体钢生产工艺有什么特点? 70
93.什么是Q&P钢? 72
94.Q&P钢连续退火工艺有什么特点? 73
95.Q&P钢与马氏体钢有什么区别? 74
96.如何选择Q&P工艺参数? 74
97.如何选择Q&P钢的成分? 75
98.什么是中锰钢? 75
99.中锰钢的化学成分有什么特点? 76
100.中锰钢的生产工艺有什么特点? 76
101.中Mn-TRIP钢的组织有何特点? 77
102.中锰钢的组织强化机理如何? 78
103.什么是热成形钢? 78
104.热成形钢的化学成分有什么特点? 80
105.热成形钢板的退火工艺有什么特点? 81
106.热成形钢对镀层有什么要求? 82
107.热成形钢对热成型工艺有什么要求? 83
第二章 轧钢生产工艺 86
第一节 热轧生产工艺 86
1.板坯加热温度对冷轧产品力学性能有什么影响? 86
2.热轧工艺对冷轧产品铁素体的晶粒有何影响? 86
3.热轧工艺对渗碳体形态有何影响? 87
4.不同的温度组合会有怎样不同的结果? 87
5.如何选择终轧温度和冷却速度? 88
6.如何选择罩退产品的卷取温度? 88
7.如何选择连退产品的卷取温度? 89
8.热轧带钢质量的主要指标有哪些? 90
9.如何提高除鳞效果? 90
10.带钢的厚度偏差产生的主要原因有哪些? 91
11.带钢的宽度偏差产生的主要原因有哪些? 91
第二节 酸洗生产工艺 92
12.为什么要对热轧板进行酸洗? 92
13.去除氧化皮的方法有哪些? 92
14.带钢表面氧化铁皮的结构是怎样的? 92
15.典型的酸洗工艺流程如何? 93
16.拉矫破鳞的工艺原理如何? 93
17.酸洗去除氧化皮的工艺原理如何? 94
18.酸洗后为什么要进行水洗? 94
19.如何选择酸洗所用的酸? 95
20.浅槽酸洗有何特点? 95
21.紊流酸洗有何特点? 96
22.带钢酸洗机组的主要形式有哪些? 97
23.推拉式酸洗生产线有何特点? 97
24.连续式酸洗生产线有何特点? 98
25.酸洗-冷轧联合生产线有何特点? 99
26.带钢酸洗会产生哪些缺陷? 99
第三节 冷轧生产工艺 101
27.冷轧生产有什么特点? 101
28.按辊系结构分,冷轧有哪些主要形式? 101
29.按轧制的形式分,冷轧机有哪些主要形式? 102
30.冷轧机组由哪些部分组成? 103
31.轧机机架由哪几部分组成? 103
32.轧机的检测仪表有哪些? 104
33.可逆式冷轧工艺有什么特点? 104
34.连续式轧制工艺有什么特点? 105
35.全连续式轧机工艺有什么特点? 106
36.酸连轧式冷轧工艺有什么特点? 107
37.为什么要对带钢的厚度进行检测? 108
38.什么是厚度自动控制(AGC)系统? 108
39.为什么要对带钢的板形进行控制? 109
40.如何对带钢的板形进行测量? 110
41.带钢的板形与哪些因素有关? 110
42.如何设计轧辊的原始辊形? 111
43.如何进行实际辊形的控制? 111
44.四辊轧机是如何控制板形的? 112
45.六辊HC轧机是如何控制板形的? 112
46.CVC轧机是如何控制板形的? 114
第三章 镀锌生产工艺与设备 116
第一节 镀锌前处理和退火设备 116
1.怎样提高电解脱脂的效果? 116
2.碱液磁过滤设备的构成与技术原理如何? 117
3.对连续退火燃烧技术有什么新的要求? 119
4.影响氮氧化物产生的因素有哪些? 119
5.常用的“高温低氮”燃烧技术有哪些? 120
6.烟气外循辐射管的结构和原理如何? 121
7.双P型辐射管的结构和原理如何? 122
8.直焰炉为什么重新被人们所重视? 123
9.直焰炉如何进行布置设计? 124
10.还有哪些降低氮氧化合物的措施? 125
11.怎样防止炉内因为喷气引起的炉灰? 125
12.高频感应加热的原理如何? 126
13.炉内带钢温度测量会受到哪些因素的影响? 127
14.如何准确测量带钢的温度? 127
15.镀锌线用辐射高温计有几类? 128
16.退火炉露点的控制有什么意义? 128
第二节 热浸镀锌设备 129
17.怎样提高锌锅温度的控制精度? 129
18.锌锅升降装置有什么作用? 131
19.无芯感应锌锅有什么特点? 131
20.锌锅辊系常用的喷涂方法和材料有哪些? 132
21.怎样提高锌锅辊系刮渣器的效果? 134
22.锌锅辊系用轴承的失效原因有哪些? 134
23.常用的锌锅辊系轴承材料有哪些? 135
24.锌锅辊系轴承采用什么方法加工? 136
25.常用锌锅辊系轴承轴套和轴瓦有哪些装配形式? 137
26.常用锌锅辊系轴承与辊臂有哪些连接形式? 137
27.带钢表面的白线状缺陷是什么原因产生的? 140
28.怎样采用炉鼻加湿控制锌灰的产生? 141
29.怎样通过炉鼻内气体过滤控制锌灰的产生? 142
30.怎样使用锌泵将炉鼻内的杂质排出? 143
31.电磁稳定装置是怎样防止带钢振动的? 144
32.带钢气垫防振器的原理如何? 146
33.怎样提高镀后冷却速度? 147
34.怎样防止镀后冷却风箱造成的带钢飘动? 148
35.举例说明解决带钢飘动问题? 149
36.镀锌板表面高压水清洗系统有什么作用? 151
37.自动辊面擦拭器有什么优点? 151
第三节 带钢热镀锌工艺 152
38.汽车板对表面质量有什么要求? 152
39.锌锅内成分和温度是怎样分布的? 153
40.锌锅含铝量是怎样影响铁溶解在锌液中的? 154
41.锌锅含铝量是怎样抑制带钢与锌液的反应的? 155
42.锌锅含铝量与镀锌层含铝量有什么关系? 157
43.怎样提高锌锅内有效铝含量? 157
44.锌锅温度和成分的波动对锌渣的产生有何影响? 158
45.带钢热镀锌工艺参数设定的原则是什么? 159
46.锌锅温度控制的依据是什么? 160
47.怎样进行锌锅温度的动态精准控制? 161
48.怎样保证带钢入锅温度的精确性? 161
49.怎样进行带钢温度的动态精准控制? 162
50.怎样解决与镀锌工艺参数相关的产品缺陷? 163
51.为什么要采用镀锌附着量的数学模型控制? 164
52.影响镀锌量的主要因素有哪些? 164
53.采用镀锌附着量数学模型控制的原理如何? 165
54.怎样采用大数据的方法进行镀锌量的精确控制? 166
55.采用大数据进行镀锌量的精确控制有什么优越性? 167
第四节 高强钢镀锌板生产工艺 167
56.在镀锌线生产DP高强钢有哪两种工艺路线? 167
57.在镀锌线上如何生产TRIP钢? 168
58.DP钢与TRIP钢对退火炉结构有什么特殊要求? 169
59.怎样采用高速冷却工艺生产高强钢? 169
60.什么是合金元素的选择性氧化现象? 170
61.合金元素的选择性氧化对镀锌有什么影响? 171
62.预氧化-还原工艺的原理是什么? 172
63.怎样选择预氧化的工艺? 172
64.预氧化工艺是怎样实现的? 174
65.如何进行预氧化工艺的控制? 174
第五节 合金化镀锌板生产工艺 175
66.合金化镀锌钢板有何性能特点? 175
67.合金化热镀锌钢板的生产需要增加什么设备? 177
68.合金化镀层的形成有哪几个步骤? 179
69.什么是合金化度? 180
70.怎样检测合金化镀锌板的合金化度? 181
71.影响合金化进程的主要因素有哪些? 181
72.为什么合金化镀锌板易产生镀层剥离缺陷? 182
73.怎样消除合金化镀锌板的镀层剥离缺陷? 182
74.怎样消除合金化镀锌板表面的缺陷? 183
第六节 镀铝锌硅板生产工艺 185
75.热浸镀铝锌硅板有什么特点? 185
76.镀铝锌硅生产设备主要有什么特点? 186
77.镀铝锌硅生产工艺有什么主要特点? 186
78.镀铝锌硅底渣是从何而来的? 187
79.铝锌硅渣主要是由哪些成分组成的? 188
80.铝锌硅渣主要有哪几种形式? 189
81.顶渣是怎样形成的? 189
82.悬浮渣是怎样存在于熔体内的? 190
83.悬浮游渣有什么危害? 190
84.底渣是怎样存在于锅底的? 191
85.硅含量与温度对铁的溶解度有何影响? 191
86.硅含量对底渣的形态有什么影响? 192
87.铝锌硅锭是如何生产的? 193
88.对铝锌硅锭质量有什么要求? 193
89.怎样减少铝锌硅渣的产生量? 194
90.怎样防止和处理镀锅结渣? 194
第七节 镀锌铝镁板与镀铝板的生产 195
91.热浸镀锌铝镁板镀层有哪些种类? 195
92.ZAM镀层成分是怎么确定的? 196
93.锌铝镁板的组织有什么特点? 196
94.锌铝镁板的耐腐蚀机理有什么特点? 197
95.锌铝镁板的耐腐蚀性能有什么特点? 198
96.锌铝镁板的加工性能有什么特点? 199
97.锌铝镁板的生产技术有什么特殊性? 199
98.锌铝镁的板生产有哪些难点? 199
99.锌铝镁板生产技术有哪些对策? 200
100.镀铝钢板有什么特点? 200
101.镀铝板的生产有哪些难点? 201
102.镀铝生产如何进行还原退火炉气氛控制? 202
103.如何进行热浸镀铝工艺控制? 204
104.如何进行镀铝的镀层控制和镀后冷却? 205
第四章 退火生产工艺与控制 207
第一节 连续退火炉的温度控制 207
1.连续退火炉中热量传递有哪几种基本方式? 207
2.辐射管提供的热量有哪几部分? 208
3.怎样进行带钢的热平衡计算? 208
4.怎样计算退火炉能耗? 209
5.炉温控制系统有几级? 210
6.双交叉限幅比例控制法原理如何? 210
7.双交叉限幅比例控制法有何优缺点? 211
8.如何进行烧嘴燃烧的平衡控制? 211
9.板温控制系统是怎样实现的? 212
10.脉冲控制法原理如何? 212
11.脉冲控制法有何优缺点? 213
12.如何进行空燃比的精确控制? 214
13.为什么要采用数学模型进行板温控制? 214
14.什么是数学模型控制系统? 214
15.数学模型控制系统可以达到什么效果? 214
16.数学模型系统离线仿真有哪些功能? 215
17.数学模型系统在线运行有哪些功能? 215
18.数学模型控制的流程和方法是什么? 215
19.如何进行带钢温度的计算? 216
20.带钢加热过程有哪几种优化方法? 216
21.产品变化时数学模型控制有什么特别意义? 217
22.产品变化时数学模型是怎样进行控制的? 217
23.斯坦因的换带数学模型有何特点? 218
24.CMI的换带数学模型有何特点? 219
25.赛迪换带数学模型有何特点? 220
26.赛迪换带数学模型的具体步骤如何? 220
第二节 连续退火炉张力控制 221
27.退火炉张力控制有什么特殊意义? 221
28.退火炉张力控制有什么难点? 221
29.为什么炉内带钢的张力会发生波动? 222
30.退火炉转向辊是怎样影响炉内张力的? 222
31.炉内张力波动与炉辊结瘤有什么关系? 223
32.如何防止炉辊结瘤? 223
33.为什么要使用炉内张力辊? 224
34.怎样选择炉区传动控制的速度基准辊? 224
35.炉内张力控制采用什么模式? 225
36.炉内张力是怎样分区控制的? 226
37.炉内各个张力控制区是怎样实现级联控制的? 226
38.高精度炉内张力控制模型有什么功能? 228
39.什么是炉内张力控制的加减速电流前馈控制? 228
40.什么是炉内张力控制的张力电流前馈补偿? 229
41.什么是炉内张力控制的机械损耗前馈补偿? 229
42.什么是炉内张力控制的S型速度给定算法? 229
43.炉内带钢在长度方向上的张力大小如何分布? 230
44.决定炉区带钢单位张力的根本原则是什么? 231
45.炉区带钢安全运行单位张力与宽度有什么关系? 231
第三节 连续退火的冷却工艺 232
46.现代连退工艺对冷却技术有什么要求? 232
47.连续退火冷却技术是怎样发展起来的? 232
48.液体介质冷却技术有什么特点? 233
49.辊冷技术有什么特点? 234
50.高速气体喷射冷却技术有什么特点? 234
51.高氢保护气体喷射冷却技术有什么特点? 235
52.气体喷射冷却系统设计不能忽略什么问题? 236
53.气体喷射冷却系统的喷嘴有几种形式? 237
54.气体喷射冷却系统的风箱有几种形式? 238
55.缓冷段气体喷射冷却有什么特点? 240
56.怎样防止带钢的抖动? 241
第四节 连续退火炉炉辊运行技术 241
57.为什么炉辊要设计凸度? 241
58.影响辊形选择的因素有哪些? 242
59.炉辊凸度与带钢的走偏和瓢曲有什么关系? 242
60.什么是炉辊的实际凸度? 243
61.带钢的板形对炉辊热凸度有何影响? 244
62.带钢温度对炉辊凸度有何影响? 244
63.带钢运行速度对凸度有何影响? 244
64.带钢的规格对炉辊的凸度有什么影响? 245
65.隔热板有几种形式和作用? 246
66.热凸度控制系统有何作用? 247
67.如何控制冷却段炉辊的凸度? 248
68.如何决定炉辊的表面粗糙度? 248
69.如何选择炉辊涂层? 249
70.影响带钢产生瓢曲的因素有哪些? 250
71.发生瓢曲时如何进行应急处理? 250
第五节 连续退火炉稳定通板技术 251
72.稳定通板技术包含哪些内容? 251
73.不同板形的原料对连退炉运行有什么影响? 252
74.连退炉对原料板形有什么要求? 252
75.如何对产品退火模式进行归类? 253
76.加热周期变更时各炉区要注意什么? 254
77.DP模式与低碳模式之间如何进行转换? 255
78.低碳模式与超低碳模式之间如何进行转换? 256
79.低碳或超低碳模式与BH模式之间如何进行转换? 256
第六节 罩式退火生产工艺 257
80.什么是罩式退火工艺? 257
81.钢卷在罩式退火前的预清洗处理有什么特殊要求? 257
82.如何选择罩式退火用的脱脂剂? 257
83.如何进行罩式退火前的预清洗? 258
84.如何提高涂硅和清洗效果? 258
85.罩式退火炉的结构原理如何? 259
86.罩式退火的工艺流程怎样? 260
87.罩式退火炉的传热原理如何? 261
88.为什么要采用强对流方法? 262
89.为什么要采用高氢或全氢保护气体? 262
90.罩式退火的钢卷温度如何控制? 263
91.什么是罩式退火钢卷的热点和冷点温度? 263
92.如何进行退火温度的控制? 264
93.如何确定退火工艺参数? 264
94.典型钢种的参考退火工艺参数如何? 265
95.影响退火时间的主要因素有哪些? 266
附录 268
参考文献 278
- 《高档钢板生产工艺与控制》许秀飞等编著 2018
- 《彩色涂层钢板生产工艺与装备技术》李鸿波,李绮屏,韩志勇编著 2006
- 《彩色涂层钢板生产技术问答》李绮屏,李鸿波主编 2009
- 《宽厚钢板轧机概论》陈瑛编著 2011
- 《中厚钢板生产》孙本荣等主编 1993
- 《冷轧薄钢板精整生产技术》陈龙官,黄伟编著 2009
- 《冷轧薄钢板生产 第2版》傅作宝主编 2005
- 《热轧带钢板形控制与检测》杨光辉,张杰,曹建国,李洪波编著 2015
- 《彩色涂层钢板技术》朱立,徐小连编著 2005
- 《冷连轧带钢板形控制与检测》杨光辉,张杰,曹建国,李洪波编著 2015
- 《网络互联技术手册 第2版》(美)(K.唐斯)Kevin Downes等著;包晓露等译 1999
- 《工业管道泄漏防治》阮徐狓,仉家骅编 1988
- 《高中复习丛书 化学》吴效衡 1985
- 《THE GOVERNMENT/PRESS CONNECTION PRESS OFFICERS AND THEIR OFFICES》STEPHEN HESS 1984
- 《生物化学应试习题集》李刚,马文丽主编;贺俊崎,倪菊华,王杰,王海生,杨洁副主编 2014
- 《俄汉工业产权词汇》中国专利局信息中心编译 1990
- 《PRESS》POLITICS & PUBLIC OPINION IN BIHAR 1912-1947 2010
- 《Press law》Robin Callender Smith. 1978
- 《SUING THE PRESS》RODNEY A.SMOLLA 1986
- 《THE PRESS AND AMERICA》 2222