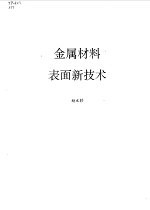
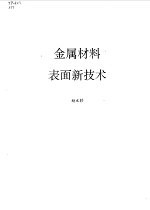
金属材料表面新技术PDF格式文档图书下载
- 购买点数:11 点
- 作 者:赵文轸著(西安交通大学)
- 出 版 社:西安:西安交通大学出版社
- 出版年份:1992
- ISBN:7560504787
- 标注页数:252 页
- PDF页数:264 页
1.1 金属表面新技术的发展概况及其在材料科学中的地位 1
第1章 绪论 1
1.2 金属材料表面新技术的目的和作用 2
1.3 金属材料表面新技术的分类 4
第2章 金属表面的物理化学特点 4
2.1 固体表面概述 6
2.1.1 固体表面与内部的不同 6
2.1.2 固体表面分子的运动状态 6
2.2 晶体的表面能及表面张力 7
2.2.1 晶体的表面自由能 7
2.1.4 表面上原子的扩散 7
2.1.3 表面原子向固体内部的扩散 7
2.2.2 表面张力 8
2.2.3 表面能和表面张力之间的关系 9
2.3 固体表面的物理吸附和化学吸附 10
2.3.1 固体对气体的吸附 10
2.3.2 固体对液体的吸附 11
2.3.3 固体表面之间的吸附 12
2.4 金属表面的特点 13
2.4.1 理想表面 13
2.4.2 一般表面 13
2.4.3 机械加工过的表面 13
3.1.1 腐蚀的起因 15
9.3 磷化膜 15
第3章 金属腐蚀的基础 15
3.1 概述 15
3.1.2 腐蚀的分类 16
3.2 金属腐蚀原理 17
3.2.1 电极电位 18
3.2.2 极化作用 19
3.2.3 腐蚀速率 20
3.2.4 电位-pH图 20
3.3 金属的钝化及表面膜 23
3.3.1 金属的表面钝化 23
3.3.2 金属表面膜 23
3.4 控制腐蚀的途径 25
3.4.1 防蚀方法的分类 25
3.4.2 防腐涂层 26
4.1.2 磨损的定义和分类 28
4.1 磨损概念 28
4.1.1 早期的摩擦理论——摩擦三定律 28
第4章 金属磨损基础 28
4.1.3 影响固体材料耐磨性的因素 29
4.2 固体表面接触的基本理论 29
4.2.1 理想光滑表面弹性接触的应力计算 29
4.2.2 实际粗糙表面对弹性接触应力的影响 30
4.2.3 实际表面的接触及接触面积 31
4.2.4 铁和其它金属接触时的粘着 31
4.3 磨损的机制 32
4.3.1 表层的粘着开裂机制 32
4.3.2 磨损的分层理论 32
4.3.3 摩擦断裂 33
4.4 耐磨设计与表面强化 33
4.4.2 抗磨材料的选择 34
4.4.1 耐磨设计 34
4.4.3 耐磨表面处理 35
5.1 概述 36
5.1.1 热喷涂方法的分类 36
第5章 热喷涂技术 36
5.1.2 热喷涂技术的特点 37
5.1.3 热喷涂技术与其它表面技术的比较 38
5.1.4 热喷涂技术发展特点 38
5.1.5 各种热喷涂方法比较 39
5.2 热喷涂的一般原理 39
5.2.1 粒子流的特点 39
5.2.2 喷涂粒子结合的动力学 41
5.2.3 涂层的形成 41
5.3.1 线材火焰喷涂 43
5.3 火焰喷涂 43
5.3.2 粉末火焰喷涂 44
5.3.3 基体表面预处理 45
5.3.4 火焰喷涂的应用 46
5.4 等离子喷涂 46
5.4.1 等离子的形成及其特点 46
5.4.2 等离子弧喷涂原理 47
5.4.3 等离子喷涂设备 48
5.4.4 等离子喷涂工艺 49
5.5.1 爆炸喷涂 51
5.4.5 等离子喷涂的应用 51
5.5 爆炸喷涂和超音速喷涂 51
5.5.2 超音速喷涂 53
5.6 热喷涂用材 55
5.6.1 金属、合金及陶瓷喷涂续材 56
5.6.2 非复合型热喷涂用粉末 57
5.6.3 复合型热喷涂用粉末 59
5.7 热喷涂涂层的特性 61
5.7.1 热喷涂涂层的基本特点 61
5.7.2 防锈防蚀性能 62
5.7.3 耐磨性能 63
5.8 涂层设计 64
5.7.4 耐高温性能 64
5.7.5 热喷涂涂层的改质 64
5.8.1 喷涂工艺的选择原则 65
5.8.2 根据使用条件设计热喷涂层 65
5.8.3 喷涂材料的选择原则 68
第6章 热渗镀技术 71
6.1 概述 71
6.1.1 粉末包镀法 71
6.1.2 流化床法 72
6.1.3 热浸法 72
6.1.4 熔烧法 72
6.1.5 盐浴法 72
6.1.6 气渗 72
6.2.1 渗层形成的条件 73
6.1.7 复合渗 73
6.2 热渗镀原理 73
6.2.2 渗层形成机理 76
6.2.3 渗层组织特点 76
6.2.4 热渗镀速度 77
6.3 热镀锌 79
6.3.1 热镀锌的方法 79
6.3.2 热镀锌层的性能 80
6.3.3 热镀锌的应用 80
6.4 热渗镀铝 80
6.4.1 渗铝的方法 80
6.5 渗铬 82
6.5.1 渗铬的方法 82
6.4.2 渗铝层的性能 82
6.4.3 渗铝的应用 82
6.5.2 渗铬层的组织与性能 84
6.6 渗硼 85
6.6.1 渗硼的方法 85
6.6.2 渗硼层的组织与性能 86
6.6.3 渗硼的应用 86
6.7.2 渗钛 87
6.7 渗其它元素 87
6.7.1 渗钒 87
6.7.4 渗铍 88
6.7.3 渗钼 88
6.8 二元与多元共渗 89
6.8.1 多元共渗的特点 89
6.8.2 多元共渗对渗层性质的影响 89
6.9 等离子渗碳 89
6.9.1 等离子渗碳原理 90
6.9.2 等离子渗碳的特点 91
6.9.3 等离子渗碳技术及其应用 92
7.1.1 几个重要概念 95
7.1 电镀理论基础 95
第7章 特种电镀技术 95
7.1.2 金属的电沉积机理 97
7.1.3 电结晶过程中的晶体生长 98
7.1.4 影响镀层质量的因素 99
7.2 合金电镀 101
7.2.1 合金电镀的特点及分类 101
7.2.2 合金电镀的规律 103
7.2.3 影响合金镀层的因素 106
7.3 复合电镀 107
7.3.1 复合电镀的特点 107
7.3.2 复合镀层沉积机理 108
7.3.3 复合镀层的现状与将来 109
7.4 电镀非晶体 111
7.4.1 概述 111
7.4.2 非晶态材料的构造 111
7.4.3 非晶体合金及其特性 112
7.4.4 非晶体镀膜基础 113
7.5 电刷镀 115
7.5.1 概述 115
7.5.2 刷镀的原理与特点 115
7.5.4 刷镀溶液 116
7.5.3 刷镀电源 116
7.6.1 镀铁原理 117
7.5.5 刷镀工艺简介 117
7.6 低温镀铁 117
7.5.6 刷镀技术的应用 117
7.6.2 镀铁工艺 118
7.6.3 镀层性能及影响因素 119
7.7 非金属电镀 120
7.7.1 非金属表面金属化 120
7.7.2 可镀塑料的选择 121
7.7.3 塑料电镀工艺 121
7.7.4 非金属电镀的应用 121
8.1 概述 124
第8章 化学镀 124
8.2 化学镀基本原理 125
8.2.1 还原剂的电化学行为 125
8.2.2 化学镀的速度 127
8.3 化学镀镍 128
8.3.1 次磷酸盐型镀液沉积机理 128
8.3.2 槽液及其影响因素 129
8.3.3 Ni-P化学镀层 131
8.4 化学镀钴 133
8.3.4 Ni-B化学镀层 133
8.4.1 钴的化学镀液及反应机理 133
8.4.2 钴镀膜的性质 134
8.5 化学镀铜 135
8.6 锡、金、银等金属的化学镀 136
8.6.1 化学镀锡 136
8.6.2 化学镀金 136
8.6.3 化学镀银 137
8.6.4 其它金属的化学镀 137
第9章 化学转化膜技术 139
9.1 概述 139
9.1.1 转化膜形成的基本方式 140
9.1.2 不同金属的化学处理剂 140
9.1.3 转化膜的基本用途 140
9.1.4 转化膜的主要施工方法 141
9.2 化学成膜的基础理论 141
9.2.1 磷酸盐膜化学反应机理 141
9.2.2 铬酸盐膜化学反应机理 146
9.2.3 草酸盐膜化学反应机理 147
9.2.4 铝的阳极氧化原理 148
9.2.5 化学氧化原理 151
9.3.1 假转化型磷化(非成膜溶液的磷化) 151
9.3.2 转化型磷化(成膜型溶液的磷化) 155
9.4 铬酸盐膜 156
9.4.1 铬酸盐膜成膜工艺 156
9.4.2 铬酸盐膜的性质 157
9.5.1 铝的阳极氧化工艺 160
9.5 铝的阳极氧化工艺及性质 160
9.5.2 铝的阳极氧化膜的性质 161
9.6 化学氧化 163
9.6.1 钢的化学氧化 163
9.6.2 铝及铝合金的化学氧化 163
9.6.3 铜及铜合金的化学氧化 164
9.7 草酸盐钝化 164
10.1 金属表面着色机理 167
10.1.1 电解发色法 167
第10章 金属表面彩色技术 167
10.1.2 染色浸渍着色法 169
10.1.3 电解着色法(二步法) 169
10.2 铝和铝合金的着色 172
10.2.1 电解发色法 172
10.2.2 氧化膜染色法 172
10.2.3 电解着色法 173
10.2.4 采用周期换向电流所得的铝氧化层的特殊着色法 174
10.3.1 铬酸盐膜的彩色 175
10.3 铬酸盐及磷酸盐钝化膜的彩色 175
10.2.5 用阳极氧化法在铝表面生成红宝石膜 175
10.3.2 磷化膜的彩色 176
10.4 化学法生成彩色氧化膜 176
10.5 铜与铜合金的着色 178
10.5.1 紫铜着色 178
10.5.2 黄铜着色 179
10.6 不锈钢的着色 179
10.6.1 工艺概况 179
10.6.2 不锈钢的自然发色法 179
11.1.2 涂料的性能及特点 182
11.1.1 涂料及其进步 182
11.1 概述 182
第11章 新型涂料及涂装技术 182
11.1.3 涂料的基本组成 183
11.1.4 涂料的分类 184
11.2 高分子涂料成膜机理 185
11.2.1 涂膜形成的物理化学变化 185
11.2.2 非桥接型成膜 185
11.2.3 桥接型涂料的成膜 187
11.3.1 涂膜对介质的屏蔽作用 190
11.3 涂膜防护机理 190
11.3.2 电解质对涂膜的渗透机理 191
11.3.3 防锈颜料的防蚀机理 193
11.3.4 涂膜的综合防蚀作用 193
11.3.5 涂膜的破坏机理 193
11.4 新型涂料 195
11.4.1 一般涂料简介 195
11.4.2 水溶性涂料 197
11.4.3 粉末涂料 198
11.4.4 元素有机聚合物涂料 198
11.4.6 特殊用途的涂料 200
1.4.5 橡胶涂料 200
11.5.1 一般涂装方法简介 203
11.5.2 静电涂装法 203
11.5 新型涂装方法 203
11.5.3 电泳涂装法 204
11.5.4 粉末静电喷涂法 206
11.5.5 其它粉末涂覆方法 207
12.1 概述 209
12.1.1 PVD法 209
第12章 气相沉积 209
12.1.2 CVD法 210
12.2 真空蒸镀 210
12.2.1 蒸镀原理 211
12.2.2 不同的蒸发源 212
12.2.3 蒸镀过程 213
12.2.4 真空蒸镀的应用 213
12.3 阴极溅射 215
12.3.1 阴极溅射的基本原理 215
12.3.2 溅射方法 216
12.3.3 溅射用气体 219
12.3.4 阴极溅射的特点 220
12.4 离子镀(IP) 221
12.4.1 离子镀的原理与种类 221
12.4.2 蒸发条件对镀层性能的影响 222
12.4.3 离子镀设备 222
12.4.4 离子镀的应用 223
12.4.5 离子镀的特点 224
12.5.1 工艺原理 225
12.5 化学气相沉积(CVD) 225
12.5.2 工艺方法 227
12.5.3 CVD沉积层的性能 229
12.5.4 CVD技术的新发展 230
第13章 激光束、离子束及电子束技术 233
13.1 概述 233
13.2 激光束、离子束的能量沉积 234
13.2.1 激光束与金属的交互作用 234
13.3 激光器和激光热处理 236
13.3.1 激光器的种类 236
13.2.2 激光束与半导体的交互作用 236
13.2.3 离子束辐照 236
13.3.2 激光热处理中的几个问题 237
13.3.3 激光热处理的特点 238
13.3.4 激光热处理在工业生产中的应用 239
13.4 激光表面合金化 239
13.4.1 表面冶金学原理 240
13.4.2 激光表面合金化举例 241
13.5.1 离子注入技术的优缺点 243
13.5.2 离子注入工艺 243
13.5 离子注入技术的工艺特点 243
13.5.3 离子注入改性的一般机理 244
13.6 离子注入技术的应用 245
13.6.1 用离子注入改变材料的摩擦磨损性能 245
13.6.2 离子注入对疲劳性能的影响 246
13.6.3 离子注入在腐蚀工程中的应用 247
13.6.4 离子注入——研究合金基础理论的工具 248
13.6.5 离子注入发展动向 249
13.7 电子束技术 249
13.7.1 能量沉积 249
13.7.2 加热和冷却 250
13.7.3 电子束表面改性 250
- 《金属表面处理技术》苗景国主编 2018
- 《金属表面强化技术 金属表面工程学》沈阳工业大学,朱荆璞主编 1989
- 《金属材料表面新技术》赵文轸著(西安交通大学) 1992
- 《高等学校试用教材 金属表面强化技术-金属表面工程学》朱荆璞 1989
- 《金属材料表面技术原理与工艺》杨川,高国庆,崔国栋编著;吴大兴审 2014
- 《金属表面处理技术》王学武主编 2008
- 《金属材料表面强化技术的新进展》朱维翰等编译 1992
- 《金属表面磷化技术》唐春华编著 2009
- 《金属表面抛光技术》李异,刘钧泉,李建三等编著 2006
- 《金属表面处理新技术》阎洪编著 1996
- 《金属材料表面新技术》赵文轸著(西安交通大学) 1992
- 《修复工程学》王汉功,赵文轸主编(西安交通大学) 2002
- 《机械零件修复新技术》赵文轸,刘琦云编著(西安交通大学) 2000
- 《材料表面工程导论》赵文轸主编(西安交通大学) 1998
- 《中华古国古都》张轸著;郑久平责任编辑 1999
- 《国民革命军北伐》凌轸著 1948
- 《决死》先轸著 2010
- 《武则天评传》赵文润,王双怀著(陕西师范大学历史文化学院) 1993
- 《旅行摄影 光与色彩篇》吴大轸著 2001
- 《远征军日记》先轸著 2009